Table of Contents
Managing inventory is a significant daily problem that still occurs frequently in the business. One of the problems is stock availability.
Based on market surveys, out-of-stock causes a loss of revenue of up to 44%.
Maintain stock availability is done not just by restocking when the stock is low or depleted, but also choosing the right time to replenish stock. Unfortunately, there are still many businesses that only rely on instinct in doing so. Even though the result sometimes can’t meet the actual market needs.
Imagine buying additional stock when there is still much stock in the warehouse. Inventory becomes excess, thus increasing storage costs that you have to spend. Not to mention the risk of product expiration because it hasn’t been out of the warehouse for a long time.
However, suppose you wait to restock until you are entirely out of stock. In that case, potential sales will likely be lost, resulting in dissatisfied customers. This can make them switch to competitors, you know!
To get around this, determining the reorder point is a solution.
What is the reorder point?
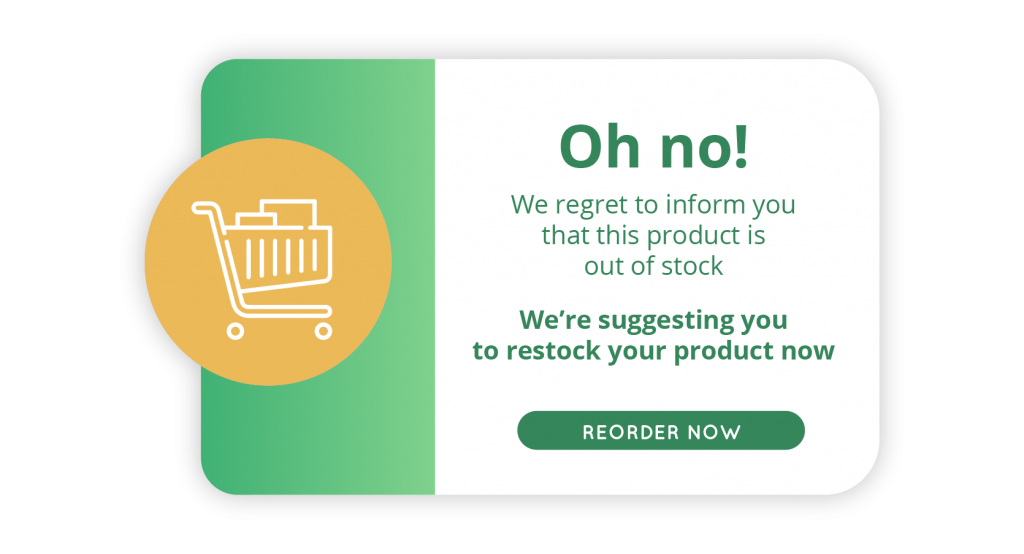
Reorder level, another name for reorder point, is the minimum limit for the quantity of a product before it runs out of stock. The product must be reordered when the amount is equal to or below that point.
For example, if the reorder point for product A is 200 pcs, then when the stock for product A is left < 200 pcs, the product must be restocked.
The reorder point functions to optimize business inventory management. With this, you can ensure restocking is done on time, and customer demands are met without running out of stock.
The primary purposes of the reorder point are…..
- Preventing stock running low/out of stock when demand is high
- Avoiding supplies of goods piling up even though demand is low
- Optimizing inventory turnover
- Minimizing production costs
How to determine the reorder point?
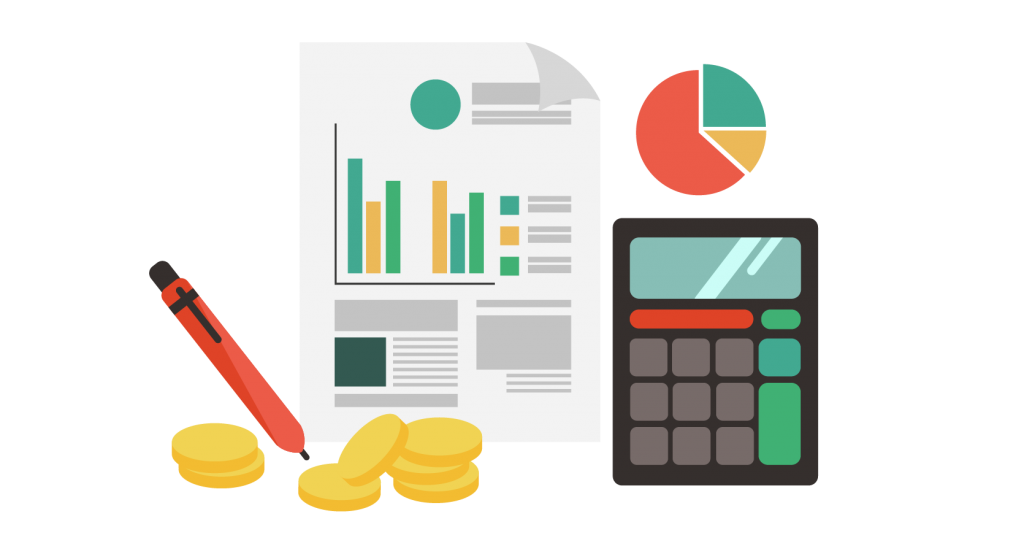
Reorder point is determined by two main factors: Lead Time Demand & Safety Stock.
1. Determine Lead Time Demand
Lead time demand is the period (days) your business needs to order stock, from initiating the order until the receiving the goods.
Lead Time Demand = Lead Time x Average Sales per Day
Example: You order product A stock from a manufacturer, and the producer has to make your order for three days. After the order is made, it needs to be packaged for one day. Then the delivery takes four days to arrive at your address. After arriving, you need one day to pack before sending it to the customer. Your lead time = 3+1+4+1 = 9 days.
Then, if your business sells an average of 12 pcs of product A per day, the Lead Time Demand you need is = 9 days x 12 pcs = 108 days.
2. Determine Safety Stock
Safety stock is a reserve or additional stock to ensure adequate order fulfillment.
Safety Stock = (Highest Daily Sales x Longest Lead Time) – (Average Daily Sales x Average Lead Time)
Example: The average daily sales of product A are 12 pcs. However, sometimes when sales are high, product A can sell up to 30pcs. At the same time, the required lead time is usually nine days. However, if something unplanned occurs, it can be up to 20 days. Then your safety stock should be = (30 x 20) – (12 x 9) = 492 products.
3. Calculate Reorder Points
Reorder Point = Lead Time Demand + Safety Stock
If taken from the previous case example, your reorder point is 600 products (108 days + 492 products).
This means you can restock when the remaining stock is 600 or less than that.
Determining the reorder level is very important for the development of the business that you manage. So, you can easily follow the steps above to select the reorder level for each product.
Using inventory management software like Distri can also make it easier for you to manage business inventory.
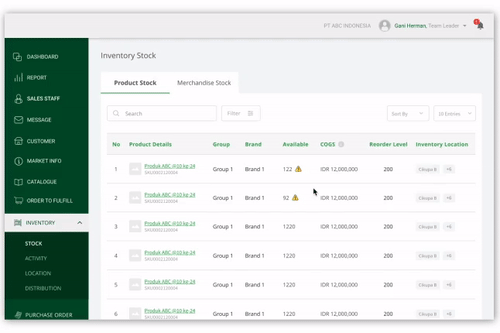
With the distribution level reorder feature, you can determine the reorder point for each product. A reminder for restocking will automatically appear when the remaining stock is equal to or less than the predetermined reorder level. As a result, you don’t need to worry about missed restocks, which will hamper sales.